Turning manufacturing data into strategic assets
- Aishwarya kansakar
- Sep 24, 2024
- 3 min read
Updated: Nov 13, 2024

In today’s fast-evolving manufacturing landscape, data is as valuable as any physical asset. Yet, many manufacturers struggle to harness its full potential because information remains locked within departmental gaps, fragmented across different systems. This disjointed structure prevents a unified view of operations, creating barriers to informed decision-making and efficient production. To truly leverage data, manufacturers need a comprehensive approach to data integration that transforms isolated information into actionable insights. Syncrowin’s data integration platform is designed to address this challenge, empowering manufacturers to convert operational data gaps into strategic assets.
The Problem with Operational Data Gaps in Manufacturing
Operational data gaps occur when information is isolated within individual departments or systems, limiting its accessibility and usability. In manufacturing, this can mean production metrics held in one system, maintenance records in another, and energy usage data in yet another. When data cannot be easily shared or analysed collectively, decision-makers miss out on the holistic view needed to identify trends, uncover inefficiencies, and optimise processes.
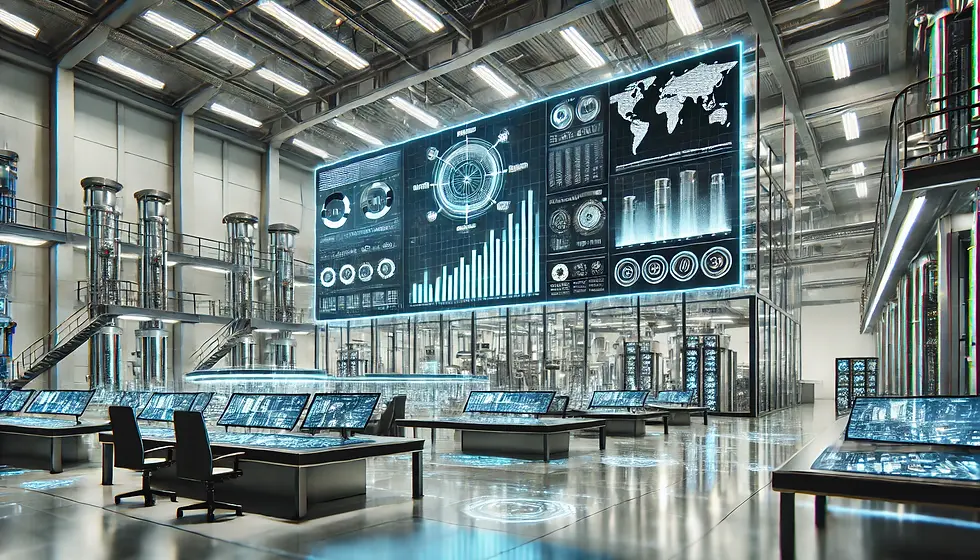
The impact of operational data gaps is significant
Limited Operational Insight: Without a unified data view, understanding the true state of operations is difficult, leading to incomplete or delayed insights.
Higher Downtime: When data is disconnected, the root cause of equipment issues is harder to identify, prolonging downtime and impacting productivity.
Increased Costs: Isolated data increases the likelihood of redundant processes, suboptimal asset use, and inefficient energy management, driving up operating expenses.
Syncrowin’s Approach to Breaking Down Operational Data Gaps
Syncrowin tackles these issues by consolidating data across the entire manufacturing ecosystem, from production lines to maintenance and energy management systems. Syncrowin’s platform ingests, organizes, and enriches complex datasets, creating a single, centralized source of truth. This enables manufacturers to make data-driven decisions based on a complete, holistic view of their operations.
Key Elements of Syncrowin’s Data Integration Strategy
Unified Data Platform: Syncrowin’s platform gathers data from diverse sources and integrates it into a single, accessible platform.
Data Enrichment: Raw data alone can be difficult to interpret. Syncrowin’s solution goes a step further by enriching data with contextual information.
Advanced Analytics and AI: With AI-powered analytics, Syncrowin identifies patterns and trends within the data, uncovering insights that may otherwise go unnoticed.
Customisable Dashboards and Reporting: Syncrowin’s platform allows manufacturers to tailor dashboards and reports based on specific operational needs.
Real-World Impact - Turning Data into Strategic Assets
Syncrowin’s approach to data integration enables manufacturers to transform fragmented data into powerful strategic assets. Here’s how real-world manufacturing environments benefit:
Better Asset Management
By consolidating data from maintenance records, equipment sensors, and production logs, Syncrowin enables manufacturers to gain a comprehensive view of asset performance. This unified view makes it easy to identify patterns of wear, predict maintenance needs, and prevent unexpected breakdowns. For example, a manufacturer using Syncrowin noticed a correlation between certain temperature thresholds and machine downtime. With this insight, they proactively adjusted operating conditions, extending equipment life and improving reliability.
Lower Downtime and Faster Issue Resolution
With all data available in one platform, manufacturers can quickly diagnose the root causes of downtime events. Syncrowin’s platform aggregates information from multiple sources—such as sensor readings, maintenance logs, and operator inputs—allowing for faster, more accurate troubleshooting. One client was able to reduce unplanned downtime by 15% by using Syncrowin’s AI-driven diagnostics to spot potential failures early and schedule maintenance accordingly.
Enhanced Production Efficiency
Syncrowin’s enriched data insights empower manufacturers to optimize production processes, reduce waste, and improve efficiency. In one case, a manufacturer realized that a certain batch variation was responsible for frequent quality issues, leading to costly re-runs. Syncrowin’s platform enabled them to pinpoint this issue and adjust raw material usage in real time, reducing rework by 20% and improving overall throughput.
Why Syncrowin’s Approach is Essential for Modern Manufacturing?
In a competitive global market, manufacturing leaders cannot afford to let valuable data remain underutilized. Syncrowin’s approach to breaking down operational data gaps transforms isolated data into strategic assets, providing manufacturers with the insights needed to drive efficiency, reduce costs, and improve decision-making.
Syncrowin’s platform not only brings data together but also enriches it with context, ensuring that manufacturers have a deep, actionable understanding of their operations. From better asset management to reduced downtime and enhanced production efficiency, Syncrowin enables manufacturers to turn data into a powerful advantage.
The future of manufacturing lies in seamless, integrated data solutions. By adopting Syncrowin’s platform, manufacturers can unlock the full potential of their data, positioning themselves to stay ahead in a rapidly evolving industry. Embracing data as a strategic asset isn’t just a smart move; it’s the key to sustainable growth and global competitiveness.
Commentaires